30th
August
2009
Deburred the nose skins, main ribs, and hinge bracket pieces for both flaps, as well as edge-finished the spars and skins. Remaining work before primer is deburr all skins, and countersink the TE wedge and spars.
Hours: 4.4 | Posted in Flaps |
29th
August
2009
Taking a break from deburring flap parts, I decided to knock out one small task remaining on the wings — install of the pitot tube mount. I’m not sure yet whether or not I’ll be initially installing a heated pitot (primarily to save the extra cost of the heated tube, though provisions would be made to add it later as part of an IFR upgrade), but I came across a Gretz pitot mount for sale via RivetBangers, and bought it. This unit has a mounting bracket that installs permanently to the wing, but the mast itself is held in place via four #8 screws, so is removable for service, or simply to keep from banging shins against it. The install is really pretty easy, once you determine where it’s going to be mounted. There’s plenty of discussion on that in the forum archives–accuracy generally isn’t affected as long as the pitot is not in the propwash, so the choices come down to things like how close is it to the tie-down rings, tube routing in the wing, etc. I chose to go with a common location, and the once described in the plans — mounting to the outboard side of the rib just outboard of the aileron bellcrank access plate, on the left wing.
The bracket comes pre-cut, and pre-bent with a joggle to clear the main spar flange. I fabricated the reinforcement angle that runs fore-aft along the rib out of a trimmed-off piece of stiffener from some control surface or another (I keep a pile of trimmings, anything large enough to reasonably have a chance of use elsewhere for a bracket or whatever). Cleco clamps hold everything in place and square for drilling, then I drilled the bracket to the spar. Adjusted the plate to sit even with the rib by using a piece of aluminum sheet to align them, then clamped that in place and drilled the angle to the rib. On the bench, I marked and drilled the skin-to-bracket hole pattern, and drilled the angle to the bracket.
Clecoed the drilled bracket to the backside of the wing skin using the main spar rivet holes, and back-drilled the holes in the skin, then cut and filed the center mast hole to size, using the mast itself to test fit. Disassemble and deburr everything, then dimple the holes as appropriate. I’ll prime these parts along with the flaps, then rivet the bracketry to the rib; the rest will get riveted along with the bottom skin.
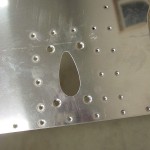
Hours: 1.4 | Posted in Accessories & Mods |
29th
August
2009
Attached the left flap nose skins, drilled the skins, and inserted/drilled the trailing edge. Then disassembled the left flap, and got to work deburring flap parts…much like the wing nose ribs, the ribs for the flaps have numerous little tabs on them, and the main ribs taper into a very tight gap at the aft end, making the process more of a pain than usual (sometimes quite literally, as the attempt to slide a finger into that narrow aft end can remove skin). I got through all of the hole deburring on the hinge assemblies, ribs, and inboard end pieces before going slightly nuts and needing a deburring breather.
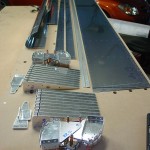
Still hoping to wrap the wings (with the exception of bottom skins and tips) before school starts in earnest after Labor Day…which may or may not actually be possible.
Hours: 4.6 | Posted in Flaps |
27th
August
2009
Hours: 1.5 | Posted in Flaps |
25th
August
2009
Weighted down and clamped the right flap flat with a pair of 2×4′s, several buckets of clecos, and a bag of pea gravel, then proceeded to attach the nose skins. Double-checked flatness, inserted the trailing edge wedge, and drilled the TE to the table. I’ll need to finish this flap to the point of disassembly before continuing with the left flap, since the opposite flap’s TE wedge is used to locate the wedge for drilling, and the right wedge is now securely clecoed in place.
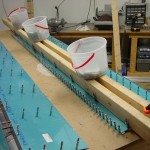
Also looked through the book, and, failing to find a specific notation to install the bushings into the flap brackets, decided they must have been part of the “assemble bracket per drawing” instruction. So, I pressed them into place using a C-clamp and block of wood.
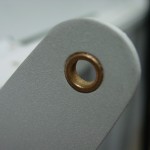
Hours: 1.6 | Posted in Flaps |
24th
August
2009
Snuck out to the shop for a bit tonight and drilled the ribs to the spars, then the bottom skins to the ribs. Clecoed on the top skins and hung the nose skins from the bottom of the spar. Need to weight these guys down before clecoing the nose skins in place…must…stay…flat…
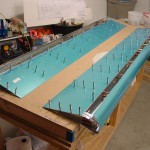
Hours: 0.9 | Posted in Flaps |
23rd
August
2009
Hours: 5.4 | Posted in Flaps |
23rd
August
2009
Finished up the ailerons by drilling the brackets to the spars, then bolting them in place. Those bolts/nuts are hard to get at with even a small open-end wrench, so I once again had to estimate the torque by “feeling” the torque wrench and trying to apply the same force to the bolt. Spot-primed where the tigthening process had scuffed some primer off, and added torque-seal to all the bolts. Messed around attaching them to the wing, and left them attached for storage; not all the attach hardware is in place, and none is tight, as the book seems to indicate that they’ll come off again in the process of fitting the bellcrank & pushrods.
The up travel on the aileron is limited by contact in the hinge brackets (later by the physical stop, once installed); down travel seems to be limited by the nose of the aileron contacting the bottom of the top wing skin/gap fairing. This is the same on both sides and appears to be normal, but I don’t have a tool handy right now to measure the up/down travel to verify things are to spec.
Ailerons are done!
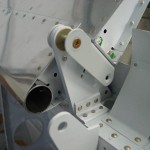
Hours: 2.4 | Posted in Ailerons |
22nd
August
2009
A good long day (and a beautiful weather day, at that) with ailerons. Started off by finished up the deburring, drilling, dimpling, countersinking, and the like remaining from yesterday’s session. Followed that up with an etch-and-prime lunch, wherein I managed to tear a hole in my rubber etching glove with enthusiastic scotchbriting (luckily, on the final piece). The full sun really makes the priming go much faster, as the light coats dry quickly. Leaving them in the sun after they’ve dried to the touch also seems to provide a harder finish faster, allowing progress to move forward.
Let the assembly begin! I riveted the reinforcements plates to the spars, then added the counterbalance assembly, main ribs, then skins, following the recipe. Riveting of the skin-to-spar lines was easy enough with the ailerons clamped upright; standing on a short stepstool gave the right height, and the tungsten bar slips inside easily. Left first, then right.
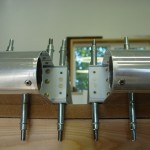
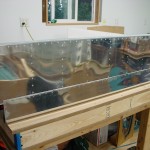
Clamped and weighted everything down to the flat table for riveting the skins to the ribs, then riveting the trailing edge closed. I used the same process I used for the empennage surfaces, where the TE rivets are squeezed entirely, not back-riveted like the manual shows. No Proseal, either. Just dropped clecoes in every hole, using a random pattern to insert them, then removed them randomly, one at a time, and squeezed a rivet in its place.
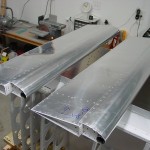
Both TE’s are straight, and the left aileron is straight, with no measurable twist. The right one might have 1/32″ or so of twist evenly across it’s length. My guess is that something got out of whack during the initial riveting process (counterbalance, perhaps?) and all the clamping & weighting couldn’t hold it true enough for the rib & TE riveting to take it out. I don’t know how big of a factor that may be, so I’ll do some reading and see if others have made notes. The manual doesn’t have a clear “x amount of twist is acceptable” like it did for the wings, but it seems like this is a small amount. It wouldn’t be difficult to build a replacement aileron at a later date, should it prove to have undesirable flying characteristics.
Hours: 10.4 | Posted in Ailerons |
21st
August
2009
No work today, so I was able to get in a long afternoon/evening session. It’s supposed to be a beautiful weekend after the last few days of clouds…thoughts of flying in the clear fall-like weather are a good motivation. Allison has been after me to schedule a flight review (my flight review currency expires at the end of August), but I haven’t yet. It’s been over a year since my last flight (7/4/08).
Bought a couple bags of pea gravel from the hardware store for weight; discovered that lead shot is expensive! The gravel was a couple bucks a bag; not as easy to handle, but cheap and gets the job done.
Finished off the drilling of the left aileron components and the trailing edge, then took it apart for deburring, and countersunk the various parts. Drilling the stainless tube went alright…used Boelube and cranked the air pressure down to 20psi on the drill for a slower speed. Didn’t even use up one bit (I had extras on hand, as I’d read reports of others going through several).
After the left one was set aside (ready for skin dimpling and priming), I brought the right aileron through all the steps the left one has seen in the past week. It’s now disassembled, awaiting deburring ans countersinking. With luck, tomorrow I should be able to get everything finished, primed and ready for assembly.
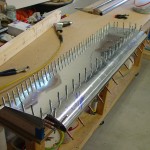
Hours: 7.0 | Posted in Ailerons |