31st
July
2010
Back from Oshkosh, it’s been a little rough getting back into the shop. Talked with lots of vendors at the show, but didn’t find the deals I was hoping for, though I got most of the information I was seeking, and made some connections. I expected to be highly motivated when we got back, but strangely the opposite happened.
Regardless, I cleaned up the disaster of a shop today, and went back to work on the canopy frame. Fit the rear bow to the rollbar, fit the side weldments along with the spacers to allow the Sikaflex bead, and drilled the splice plates. Then, the whole works is removed for deburring and riveting; I think this is also the point to install the stiffener kit and the struts (neither are mentioned in the manual). I’m using the Flyvans.com guys log as a guide for the canopy work, since I will be gluing the canopy as they did–there are many logs of the gluing method for sliders, but not many for the tipup.
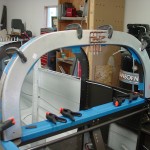
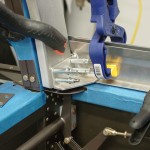
The main differences so far are that the roll bar and rear bow were built slightly narrower than plans (which meant also that the brackets were inboard, which required the fabrication of a spacer to sit outboard of the brackets, rather than filing the aft end of the bracket), and the forward splice plate of the canopy side rails, where the side rails are offset inboard by .125″ using a spacer. This is to allow for the required .125″ bead width of the glue. To make up for the inboard offset, a corresponding .125″ spacer must be installed between the side rails and the canopy skirts…I ordered a pair of the .063″ strips that are used in building the roll bar, as they’re just the right width for the job. Cutting each in half and doubling it up gives a nice .125″ spacer for the skirts, and it seems to be working well so far.
In the odd jobs category, installed the last three nutplates on the roll bar brace, having received my supply shipment from Van’s.
Hours: 5.5 | Posted in Canopy & Frame |
18th
July
2010
More work on fitting the canopy frame, which began by drilling holes in the splice plate, fabricating spacers for the goosenecks, and getting the frame positioned correctly to match the fuselage width. That done, the holes were deburred and the forward portion of the frame riveted: the bows, splice plate, spacers, and goosenecks. The whole business was then fit to the fuselage again and tweaked for fit. The holes for pivot bolts were marked with a long 1/4″ bit by peeling up the edges of the forward top skin, then the assembly removed to drill the pivot points. Bushings were pressed in with the hand squeezer…both sides turned out well, with good edge distance.
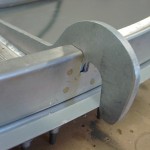
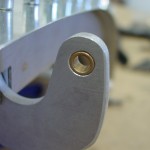
That done, it was back to the fuselage again for another round of fitting. The seal support angle needed to be trimmed to allow the canopy frame to move, and the front of the canopy skin filed down to widen the gap enough that the skin doesn’t catch the front skin and kink the edge. After another couple of on-off cycles, I think I have the front fitting decently; supposedly this all changes when the struts are fit, but I see no mention of that in the manual, so I will have to see when that’s best done. I do plan to add the canopy stop bolts that have become popular, to provide a positive forward stop to counteract the “thrust” of the struts when in the closed position
I will follow the lead of Chad Jensen and the Flyvans.com guys, filling the gaps at the outboard three holes with washers, so I put stacks of 960-10′s in there for now.
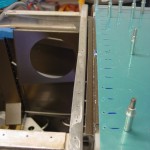
Hours: 6.1 | Posted in Canopy & Frame |
17th
July
2010
Installed various tie-wrap bases for the tailcone wiring runs, and pulled the aft nav/strobe, pitch trim, pitch servo, VOR and transponder antenna cables into the tailcone. Installed standoffs for the static line in the tailcone and secured the line, checking for clearance with the harness anchor bracket. Installed the ELT mounting bracket.
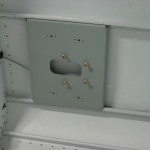
Worked on fitting the canopy frame by clecoing the skin to the forward frame weldment and fitting to the fuselage. After several on-off cycles and adjustments, it was fitting pretty well, so the splice plate was drilled to the forward bows. Removed the skin and cleaned out the chips, then re-clecoed and checked the fit on the fuselage. Fits the same, with the usual slight gaps at the left & right front sides, that require spacers under the front skin. An initial check of where the hinge holes will fall shows that the holes are almost dead center in the hinge goosenecks…I’m pleased with that, though I do need to fabricate spacers to go between the goosenecks and the forward bows (that distance is set by the holes in the skin, and mine has a gap…no biggie, it looks like a piece of .063 and .040 will fill it nicely.
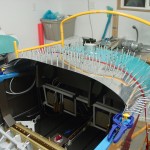
The issue at the moment with the canopy frame is that, for the outboard three holes of each side’s aft tube, the skin does not sit down to the tube…there’s quite a gap. I’ll have to read up on what others have done here, whether make spacers, omit these holes, or what. Also trying to figure out when the canopy stiffener kit should be fit, as there is no mention of it that I can find in the manual.
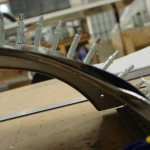
Hours: 7.6 | Posted in Canopy & Frame, Electrical |
16th
July
2010
Another session of disparate small tasks. Perhaps the less focused building sessions are what causes the feeling of being overwhelmed that builders seem to get in the end stages; there’s a hint of that here. I’m trying to wrap up some odds and ends around the fuselage before diving into the canopy work.
- Finished drilling the roll bar brace for the cover plate, and drilled it for nutplates. I didn’t have enough #6 nutplates to do all the holes, so I left a few easily accessible ones without; they’ll be easy to stick in later, when my shipment from Van’s arrives next week.
- Primed and painted the cover plate…wow, is the spray-can primer I picked up easy to use, it will come in handy for one-off bits from here to the end.
- Riveted and bolted the roll bar to the fuselage. Clecoed the structure aft of the baggage bulkhead solidly together before bolting this on, to set the correct location fore/aft. It’s difficult to get any large tools in there, and fitting the washers and nuts is a trick, too–the tool that I called the “grabber” growing up (I’m sure it has a real name…) came in very handy here, to hold the washers and nuts in the right place.
- Applied UHMW tape to the inside of the canopy latch angles, riveted them to the side skin, and assembled the rest of the latch mechanism.
- Put a strip of UHMW tape across the top of the flap motor housing, where the canopy latch tube rubs slightly.
- Mixed up a small batch of proseal and stuck the NACA vents to the side skins. (Forgot to put the screens on the fuel vents while I had it mixed up…darn!)
- Made an antenna drill template, and drilled for the Com1, Com2, and Transponder antennas. Very handy that they all use the same mount spacing (though beware, the Com antennas are longer fore/aft than the transponder). These are from DeltaPop, and though I can’t yet comment on their performance, they’re reasonably priced and quite attractive. Other users report good things, including the folks at NavWorx, who recommended the ADS-B antenna for use with their boxes (I have that antenna too, and will be prewiring for the NavWorx transceiver…). There is also an APRS antenna in the works, I believe.
- Drilled a hole for a wee rubber grommet in the aft bulkhead, to feed wiring to the rudder for nav/strobe lights. I ordered a 100-pack of 1/8″ ID grommets from McMaster Carr, because that’s the smallest pack they sell; I’m set for life now. I discovered later that SteinAir sells a kit with an assortment of different sizes… I also ordered a bunch of different tie-wrap bases including the regular square-base type and some other useful-looking ones like thru-hole mounts; having the different kinds on hand will come in handy for the electrical installation.
- Spread out a big piece of paper and drew a crude representation of an airplane on it, and looked at laying out the various wire runs through the fuselage. I want to get the pieces aft of the baggage bulkhead in place, so I can close up the aft fuselage.
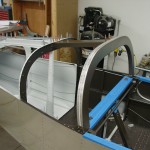
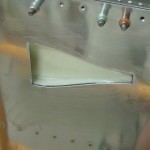
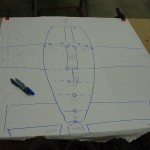
Hours: 4.3 | Posted in Cabin & Interior |
14th
July
2010
A conglomeration of cabin tasks tonight:
- Riveted the forward canopy decks to the longerons and subpanel.
- Installed the spar upright cap strips with blind rivets.
- Installed the canopy hinge blocks.
- Riveted the parking brake valve bracket to the firewall, and bolted on the valve.
- Attached the brake lines to the valve and torqued.
- Laid out, cut and drilled a removable cover plate for the bottom of the roll bar brace.
- Cleco-clamped my finger and decided to call it a night.
Hours: 3.4 | Posted in Cabin & Interior |
13th
July
2010
Today’s session was mostly about turning little parts into larger assemblies, some of which got mounted to the fuselage. Riveted together the fuel pump doghouse, roll bar brace, forward canopy decks, and subpanel left/right sections.
When the assemblies were assembled, I set about installing things…first up, the main canopy latch. After riveting on the latch bellcrank pivot bracket, the roll bar brackets, and latch weldment were bolted in place, and the latch bellcrank installed and connected to the weldment, complete with cotter pins. The side latch handle isn’t installed yet (I’m waiting on some UHMW tape to arrive), but the pushrod is assembled, and the knob screwed to the handle.
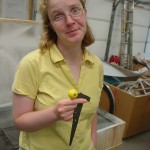
Before installing the subpanel, the firewall needed to be dimpled for the flush rivets which attach the subpanel ribs. The top two holes of each were reachable with the squeezer, but the lower three were not. I ended up using the rivets themselves as a dimple die–”pre-dimpling” the firewall with a couple taps of the gun, with the rib backed by a squeezer yoke; it then dimpled itself nicely as the rivet was driven. This worked beautifully on the rather malleable stainless firewall; I don’t know how well it would work on an aluminum piece, especially anything thick.
That done, the subpanel assemblies were inserted and clecoed, then riveted to each other, the firewall, and side bulkheads. Shooting the side bulkhead rivets required undoing one of the adel clamps securing the fuel line and gently bending it out of the way for a moment to allow access for the gun. Next, the forward canopy decks were clecoed in place. Also stuck the rudder pedals in, lest that be forgotten until access is made impossible; they’re not yet bolted down, so could be strapped up out of the way to allow for access to the lower firewall.
Tonight’s art project: cut out the templates for the NACA vent installation.
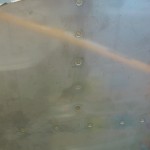
Hours: 4.9 | Posted in Cabin & Interior |
12th
July
2010
Picked up another quart of paint and sprayed the pile of parts prepped yesterday. Set to dry overnight, with some assembly on the plate for tomorrow. Also ordered some wire bushings, extra nutplates, UHMW tape, and a couple other odds and ends in preparation for wiring work.
Hours: 1.8 | Posted in Cabin & Interior |
11th
July
2010
Finished off the installation of the main canopy latch by cutting the slots in the fuselage side skin; used the traced template to drill the pilot holes, then masked the area to be cut with blue tape, made two passes with a Dremel cutoff wheel, and worked with needle files to finish it off. Not bad. Drilled the mechanism to the skin, dimpled with the pop-rivet dimpler, and countersunk the angles, before fitting the aft part of the mechanism. All in all, an easy piece of the puzzle, and it operates well. I did have to slightly enlarge the aft slot top to bottom to prevent binding and scraping of the handle; I think there is a slight bit of variation to the straightness, and I couldn’t convince it any straighter. No biggie.
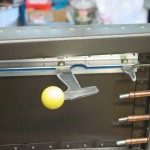
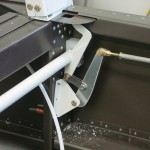
Note: when you go to rivet the little screw plate to the top of the flap motor mount channel, use flush rivets, rather than universal heads…I ended up drilling out those three AD470′s and replacing them with 426′s, because they were rubbing on the torque tube for the canopy latch. Even without the rivets, the tube rubs slightly on the channel; I think this is a common problem. I’ll probably stick a piece of UHMW tape on the channel there to avoid chafing, unless a better solution comes to light.
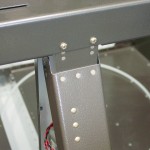
Pulled out the canopy frame to look at how it goes together; did a couple common things: filed the welds flush, chamfered the forward edge of the hinge ears, and chamfered the aft edges of the plastic hinge blocks. This allows the ears to guide themselves into the slots.
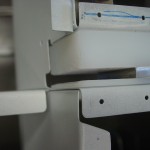
Time to check off the laundry list of little fuselage tasks to get ready for some riveting:
- Removed the latch mechanism, disassembled for prime/paint, and deburred.
- Removed the forward top skin and subpanel assembly, spot primed scuffs, and set aside. Debating whether to paint the stuff aft of the subpanel or not. (Note to self: still need to ream the outer bulkhead holes)
- Removed the roll bar and brackets for prime/paint. Deburred and cleaned up shavings from that installation; touched up paint on the trimmed corners of the seatback rests.
- Removed the mid top skin for painting; lifted one side of the aft top skin for wiring/plumbing access.
- Pulled the static line with the hole drilled in it and ran a replacement line.
- Spot primed aft bulkheads and vacuumed the aft fuselage.
Etched and primed all the removed parts; rattle-can painted a few little things, waiting on the rest–I need to pick up another quart of the Rustoleum brown, because it goes on better with the sprayer than from the cans.
The plan going forward is to run some wiring in the aft fuse, then close that up, along with the structure of the subpanel, to prepare for fitting the canopy frame.
Hours: 9.7 | Posted in Canopy & Frame |
10th
July
2010
Spent most of today working on the canopy hinges and latches. First order of business was to drill the 1/4″ holes for the pivot pins, using a 12″ drill bit I picked up. That done, I built up the mechanism that inserts and retracts the hinge pins. This required cutting off the threads and rounding the ends of the pins themselves, fabricating the pushrods, and assembling the bellcrank mechanism. The goofed-up hat channel was replaced with a shorter piece, cut from the section that was cut off before. This should work fine, since its only purpose is to hold the bellcrank…I had enough material left to pick up the top three rivets on each side. Installed the lever on the bottom of the bellcrank, but not the tube that runs aft; instead, I made a little handle that attaches to the lever, and has a tab with a hole to secure it to the subpanel. I put in a nutplate for a #8 screw to hold it there; a nice improvement would be a thumbscrew with a #8 thread, so that it would be easy to undo without having to mess with a screwdriver behind the panel. This tab will be easily reachable, since this is open to the sky when the canopy is open. (The tab idea was shamelessly stolen from another website, though I can’t remember where I saw it… Flyvans.com, also a good resource for tip-up canopy Sikaflex tips.)
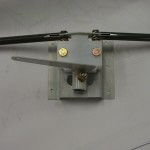
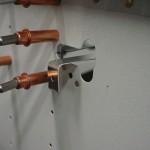
With that mechanism rigged, on to the next thing…the main canopy latch. First up is to fabricate the control lever, which allows the pilot to latch/unlatch, and also protrudes through the side skin to allow the latch to be opened and closed from outside of the plane. The upper and lower angles were fabricated, latch arms deburred and straightened, and holes drilled–bottom first, then match-drilled to the top angle. (Hint: I use my back-rivet plate as a true surface to verify that things are flush if needed for match-drilling.) I stacked up four layers of masking tape on the inside face of the angles to allow for the thickness of primer and UHMW tape to be applied later. For fun, drilled the yellow latch knob to the lever. And finally, traced the template for cutting the side skin, which I’ll get around to tomorrow.
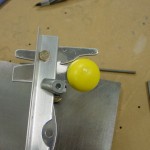
Hours: 6.2 | Posted in Canopy & Frame |
9th
July
2010
Finished up the subpanel installation by fitting and drilling the angle clips that hold the outer corners of the instrument panel to the forward canopy decks. Also drilled the center section cap strips to the vertical members; snapped off another 1/8″ angle drill bit, now I’m down to just the short stubby one. I think this results from excessive bit wobble in the cheapo angle drill attachment…next time (ha!) I’ll splurge on a real angle drill with a small head.
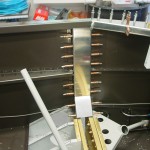
On to the canopy hinges…fabricated the plastic blocks and aluminum spacers according to plans. Apparently, the stub ribs weren’t supposed to be riveted to the subpanel yet, since they need to be out of the way for some match-drilling at this step. No big deal–I just removed the center portion of the subpanel, leaving the sides in place, and a nice open area in which to wield the drill…worked well. Once the appropriate drilling was done, the center part went back in to be drilled. I kept the top skin on for as much of this as possible, moved forward three holes when necessary to provide a gap to work/drill/see/clamp in. I wasn’t able to drill the hinge pin hole through to the stub rib, because my 1/4″ drill bit is too short, and I can’t get the drill in the correct place to make a straight hole…I’ll pick up a longer bit, which should solve the problem.
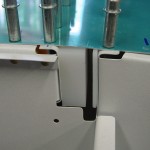
Hours: 4.7 | Posted in Canopy & Frame |