26th
May
2007
Most of the day doing yardwork with the lawnmower from… well… I found it for free on the side of the road going to work one day last year. Does that tell you anything? It mows…most of the time. That’s about all I can say for it.
Remade the HS attach angles today, with the new angle stock that I ordered along with the practice kit. This time around, I ran the edges of the stock on the sanding disc before marking the cut lines, so I could make a nice edge without the worry of removing too much material. I also used the tilt table on the sanding disc after the hacksaw to bring the edges right to the line, and to keep everything at a consistent angle. Just like Dad always said…”make the machine the expert.” A couple passes over the Scotchbrite wheel and things were looking good. Much happier at this point than I was with the old ones.
Still plenty of time for foul play though, with my old nemesis the drill press. I carefully measured & marked the hole layout, then center-punched, but this time instead of going right to the drill press, I twisted a #40 bit by hand to enlarge the centerpunch marks. I found that this really helped get things started in the right place when I went to the drill press. The holes looked good, and I remeasured the alignment hole (top center) at each step in the process to be sure. Everything was good, so I clecoed & clamped them to the HS spar. Drilled out the holes, disassembled and deburred everything.
That seemed like a good place to stop and go knock off more of the “honey-do” list, so I cleaned up the shop and organized everything. Oh-I also put a valve on the outlet of the compressor tank yesterday; that solved the overnight leak-down problem: I suspect the culprit is the $20 Menards special “air control kit”…they’re cheaply built and (obviously) has a slow leak somewhere. Regardless, this solved the problem, and will also allow for cleaning the filter bowl without having to air down the tank.
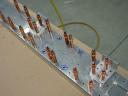
Hours: 2.0 | Posted in Horiz. Stabilizer |
25th
May
2007
Over the past couple evenings, I’ve completed the second pratice project with no major difficulties. This is a short section of control surface, and incorporates a number of techniques–flush & universal-head riveting, back-riveting, double-flush riveting on the trailing edge, rolling the leading edge, etc. I decided to mix things up and try out a number of different tools/methods for getting things done, in the interest of being more familiar with tha various options. The highlights/things learned:
- This should have been obvious (common sense!), but don’t try to save time by not building fixtures to hold things solid during riveting. They even give you a diagram of a fixture, and parts to build it, but it seemed to stand up okay on it’s own, so I gave it a shot…nope. Drilled out 4 rivets I didn’t like. Built the fixture, and life was good. A good lesson.
- I have three flush sets–a straight mushroom, a straight mushroom with a rubber ring around the face, and the swivel mushroom that everyone seems to love. So far, I’m preferring the straight set with the rubber ring. Maybe it’s just me, but I had an easier time keeping the gun where I wanted it with that one. I’m curious to try the swivel set again with a two-person rivet/buck operation–I can see where the swivel would be beneficial, and I think it could shine when the shooter is able to hold it against the surface. It tended to walk in the direction of gravity when I was one-handing it.
- Duct tape on bucking bars is a goooood thing.
I can also see why people are loving the tungsten bucking bars that are the latest rage online; every tool supplier has added them to their catalog. Bucking the skin-spar rivets down in there on the second skin is a challenge with a big bar; I ended up grinding a new face on one of the other bars, since nothing was fitting real well.
- Duct tape on squeezer yokes might also be a good thing; I noticed after the fact that I had put a couple scratches in the spar web while dimpling with the pneumatic squeezer, and had to be careful of where I was with the yoke while riveting. I might take a look at deburring those sharp edges? Something to check.
- Squeezers: The hand squeezer is easier to control, probably because of its light weight. The pneumatic sets rivets easier! I’m glad for the pneumatic (my hands, I believe, will thank me sooner than later…with some wrist pain from daily activities, I think it’s a wise choice), but I think having the hand squeezer, even the el-cheapo one I have (US Tool) will come in handy in some cases.
- My trailing edge came out pretty straight, but I could stand more practice on the double-flush rivets. I didn’t feel like they were setting well. They tended to bend over more than squish down, and some of the results left things a bit loose. I tried a .5 longer rivet in one case, and it may have helped, but still fell over to the side. I may drill these out and re-do for more practice before doing the rudder & elevators.
So that’s it for the practice projects. I had hoped to practice priming and such on this one as well, but haven’t ordered any primer yet. I’ll probably do that on Monday or Tuesday. I need to deburr and dimple the HS skins, and see how people handle the etch step and/or priming only the rivet lines on skins, with the AFS primer. (Looking at web pages, seems like most AFS users are priming the entire inner side of the skins, but inconclusive on the etch step. I wouldn’t think etching the top of the skins would be avoidable, or desired.)
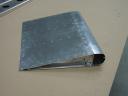
Hours: 6.0 | Posted in General |
18th
May
2007
I ordered the “RV Class Project” kit from Van’s; it comes with two projects to complete. The first is simple, sort of the ‘next step’ from the morning sheetmetal workshop we attended at OSH last summer–A narrow aluminum sheet, riveted to a piece of angle, with another sheet riveted to it. You get 20 holes to practice drilling, deburring, dimpling/countersinking, and riveting. 2 blind rivets, and 18 solid of assorted types & sizes. Pulled it out this afternoon–after cleaning up the yard in preparation for a picnic we’re hosting–and completed it in a reasonable time. Things I learned:
- This riveting thing isn’t as big of a deal as it’s sometimes feared. I over-drove a number of the rivets, mostly the smaller AD3′s, before I got the feel of the gun and how long to pull it for. I had a couple under-driven and then they ended up over-driven after I tried to give them another shot. I don’t believe I had any that would have been necessary to drill out, and I didn’t end up with any smileys or dents/dings…overall, not bad.
- Edges of sheet stock need to be rolled before dimpling…duh!
- Double-check the hole size before drilling the beginning and end of a row to cleco the rivet fan spacer into.
Overall, not a bad way to get started. I’m looking forward to trying out the squeezer & various yokes, along with the swivel rivet set, when I get into the larger practice project, which is a short section of control surface.
Also back in the saddle with flight training–we’ve had pretty strong/gusty winds here the past week or more; not too ideal for practicing pattern work, but I managed to get up for .6 with my instructor; I was happy to find that I didn’t seem to have lost as much as I feard I might have. 3 trips around & landings; the last one was fairly solid, and I got my 90-day solo endorsement renewed. Scheduled for Monday to try and get in some solo work in preparation for solo X-C; I’m not too optomistic about the winds…but that’s springtime in MN!
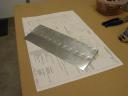
Hours: 1.5 | Posted in General |
17th
May
2007
Bought a set of files the other day, so used my short time in the shop today to clean up and deburr the inside corners of the HS spar doublers, and the small holes on the rear spars.
Hours: .3 | Posted in Horiz. Stabilizer |
14th
May
2007
My flight lesson was cancelled today because of wind (20′s gusting 30-35), and the temps were in the low 90′s, so a good day to hang out in the shop.
Started out doing some deburring on the spars & doublers, lightening holes, etc. Need to pick up some smaller files, curved/rounded, etc to dress out the inside radii on the doublers. Then cut & set up the HS cradle and built up the right side in the skin. The nose ribs took a few tries to get the hang of, fluting them to fit the proper curve. The rest of it went together nicely, the holes all lined up well and dropped into place. Reamed the holes to #40, then repeat for the left side. Remembered to put the spar doublers in on the first try this time…
Wrapped up the day by rounding the point off an old soldering iron and melting lines in the plastic sheeting. Deburring of all the skin holes is next, then dimpling. I need to order some primer & find a gun so I’m ready to shoot when that time comes.
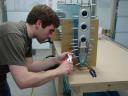
Hours: 6.75 | Posted in Horiz. Stabilizer |
13th
May
2007
Not much to report today. Having a hard time remembering to write in the log at the end of every day. I suspect this will be more of a “highlights/lowlights” journal than a blow-by-blow detailed daily report–which I think is OK, as there are plenty who have gone before and done an excellent job with that. (See the builder sites link list for a handful.)
Allison’s family was here for most of the day, then we went out in the evening and disassembled the HS skeleton I’d clecoed and drilled previously. Allison worked on deburring the spars while I did some filing on the doublers.
Hours: 1.5 | Posted in Horiz. Stabilizer |
12th
May
2007
Spent the afternoon/evening making friends with my scotchbrite wheels and pads. Rib deburring was the order of the day, I made it through the pile of main ribs without too much difficulty. Biggest deal was figuring out how to get into those teeny nooks between the main flange and the little tab flange that goes inside the spar. Then I realized I had forgotten about the nose ribs, so back to the wheel I went. Not bad, really.
Fluting was less of a big deal than I thought it would be, from the reading online I had done. I used my rivet fan clecoed into the first and last holes (thanks to whoever I stole this idea from), and clecoed to the bench so the rib hung over the edge. A pinch here, and squeeze there, and the holes were straight in no time.
That being done, it was a short step to putting something together, so I did. The HS skeleton is assembled, and it doesn’t look half bad (if I might say so myself). I was able to make the HS-909 shims easily with the belt sander, and drilled them into place. My only worry is that the holes on the little rib tabs (the rib-to-spar-to-skin holes on the fwd spar) don’t line up quite right…they’re off by 1/3 to 1/2 hole, fairly consistently. I did some reading online and found a note on someone else’s log that once this is assembled into the skin, everything lines up better. We shall soon see.
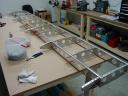
Hours: 5 | Posted in Horiz. Stabilizer |
10th
May
2007
Put the rear spars & doubler together and drilled. Which is to say, reamed. I bought into the talk about reamers being better than drills for enlarging the pre-punched holes, and was able to pick up a #30 and #40 reamer with my purchase of secondhand tools. Happy with the results so far, and my cheapo air drill seems to run fairly true, which I was concerned about. Not that I don’t still lust after that Sioux 1412 3600-rpm palm drill…
Also put the hinge brackets into place and drilled them out. I was surprised how easily the steel machined. I think part of it is that I’ve been used to working with old dull bits, and this whole “sharp” thing is sort of a novelty to me.
Hours: 2 | Posted in Horiz. Stabilizer |
4th
May
2007
Back from the trip to Alaska. It’s always nice to go “home,” even if it’s only for a few days. Our flight out of ANC (nonstop to MSP) was cancelled (5 minutes after the scheduled departure time) when the fourth flight attendant called in sick, so we ended up standing in line for a couple hours to get rebooked. We ended up bouncing through Portland, and got into Minneapolis about 6 hours after we had originally planned. Making some progress on things around the house, and the siding for the shop is on order at Menard’s (estimated delivery 3 weeks…hard to believe!), so I can take a peek at the project again. Allison is afraid that once I start, I won’t stop until it’s done. Even to eat. Apparently she’s observed some of my past projects…or else she’s been talking to Mom.
Match drilled the spars that I’d clecoed before we left, and started on the attach angles. Unfortunately, the drill press I’m using has some wobble to it, and isn’t highly precise for drilling holes, so I’m unhappy with the way the 9-hole pattern turned out. I clecoed the angles to the spar in the alignment hole, and I think they’d work fine, but I would be unhappy with them forever; they’re ugly, and I’m a perfectionist. I think I’ll order the practice kit and some ProSeal for trailing edges from Van’s, and have them throw in another piece of aluminum angle…it’s only about $6.

Hours: 1.5 | Posted in Horiz. Stabilizer |