Back from Oshkosh yesterday night: spent 3 days (Sun eve-Wed eve) there in Camp Scholler, but missed the RV BBQ, which was just a couple streets over from where we were set up. Good show, lots of sun, lots of walking. Took several dozen pictures, saw the 35-ship RV flyover on Wed morning. Walked the entire field of RV’s, but no one was really around to talk to. Not too many 9′s in attendance, but saw both Mike Schipper (my favorite paint job) and Matt Brandes‘ birds; two websites that I regularly use for reference and inspiration. Also saw lots of goodies from the vendors, including AFS’s new software for the 3000 series of EFIS’s, which looks really good: they added odometer-style numbers, changed the style of the speed & altitude tapes, added speed & alt bugs, and some other enhancements. I got to play with the display at both the AFS booth and the SteinAir booth, and was as impressed as I hoped I’d be. They’re also showing moving map, and terrain & WX are in development. [I heard that AFS is going to partner with Honeywell to develop a certified system--I hope that doesn't jack the prices on the experimental systems, or do away with the experimental models...] I also saw Icom’s new A210 radio, which is another option for an SL-40, has the same features like dual-watch, plus 10-channel recall, also has a nice display. I didn’t see any pricing, though I’m betting it’ll be somewhat less than an SL-40. Saw the Garmin 496 demo’d, nice unit, the display resolution is incredible. (Is it obvious that the panel is my favorite part to dream about?)
Also talked to several different engine folks, and the opinions on Carb/FI and autogas are all over the map. Superior will warrantee their engines (8.5:1 or less) to run on autogas, and have a 3-year warantee. ECI (supposedly having the best cylinders for corrosion resistance) has only a 1-year warrantee, and it is void if you run autogas. I talked to one gent who said that I shouldn’t have to worry too much about corrosion if the engine is in a climate like ours (ie non-coastal based), and gets exercised regularly. I still like Klaus’ Lightspeed ignition, and the Catto props look as nice in person as they do in pictures. Just some observations…
Bought some needed tools while I was at the show, so today I escaped the heat in the garage (after expending my allowance of curses for the day on mowing the lawn), and made severe progress on the rudder. I got the counterbalance rib dimpled (new #10 dimple dies), and dimpled the narrow ends of the ribs (tight-fit dimpling fixture from Cleaveland Tool, needed to grind some off the bracket to get it in close enough). Riveting everything together went very smoothly with the assistance of the 4″ no-hole yoke and the longeron yoke on the squeezer…that thing makes quick work out of a long line of rivets. I did give in and use blind rivets in the last 2 holes on the top, and the last hole on the bottom of each side (the plans allow this). It’s very narrow there, too much for even the no-hole yoke, and I tried bucking one in there with the end of a pry bar–I did more harm than good and had to drill out the rivet. Since the plans say it’s ok, I put the pops in there, figuring I’d just create a mess if I tried to get solid rivets in there. The purists would be disappointed, but I’m building this thing to fly, not win awards… I did have to trim the 4th stiffener from the bottom (both sides) to clear the center spar doubler, as was noted on another builder’s website.

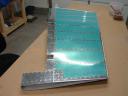
I went ahead and rolled the leading edges (fun…not!) and riveted, as well as installed the rod end bearings. After that, I gave in and hung it on the VS with some bent nails for fun. Not bad! I left the jam nuts loose on the bearings, as they will undoubtably need final adjustment after mating with the fuselage. It was nice to see the VS & rudder in assembly, though! From here, I’ll go to the elevator assembly, saving the rudder TE for later, so that I hit all the Proseal at once (I only have a single cartridge, not the mix-your-own cans.)
