14th
November
2010
With the chunk of angle for the replacement fuel tank bracket in hand, it was off to the shop to carve it up. Using the well-fitting left bracket for a template, I traced it in reverse onto the angle for the right bracket, then cut with the bandsaw–bent the angle before cutting the 1″ leg, then shaped to final size with sander and wheel. Clamped both brackets up to the tank and fuselage, and drilled from inside. The bottom hole is easy to drill, but the top hole is blocked by both a gear tower tube and the fuel vent line, which meant that the vent line had to come off, and the angle drill be used to make the hole. No problem; then the brackets are temporarily bolted up and clamped to drill the hole through both brackets. Once the wings come off, the hole will be slotted and a nutplate installed (after priming…).
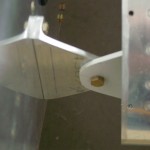
That task complete, on to the final remaining item before wing removal…installation of the flaps and pushrods, which required cutting the pushrod exit holes. I started by enlarging the holes in the side and bottom skins with a unibit to 1/2″, then connecting them in a rough shape with a round file. After the pushrod is attached to the flap and the flap to the wing, the pushrod can be inserted from the bottom and pinned to the actuator arm; then the actuator is moved up and down to check the pushrod hole. It took several rounds of removal, enlargement of the hole (Dremel sanding drums work well), and re-connection before the hole was right. I wanted to creep up on it, so as not to have a larger than necessary hole. Once everything was fitting well, I made a tracing of the hole and transferred that to the other side for a starting point…trimmed it out slightly small to allow for any difference between the sides to be taken up during the fit/enlarge process, but it should make the second side easier. Finished the rough cutting and hooked up the pushrod before calling it a night. Hope to get the flap finished and the wings pulled tomorrow, to gain Allison’s car a space in the garage again.
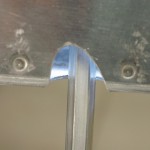
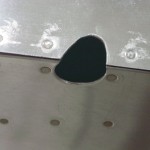
One word of caution and lesson learned: beware of the little flaps of metal that hang off the aft end of the wings at the inboard edge of the flaps. When the flap is attached, this piece tends to end up on top of the flap nose…it must be on the bottom side of the flap, or it will be pushed up between the flap and the rear spar and bent when the flaps are raised. I didn’t check this before raising the left flap, and then promptly repeated the mistake on the right flap…sigh. The bends mostly came out by hand; I’ll work them a bit more when the wings come off. At least they’re symmetrically bent now…keeps the plane flying straight! (builder joke…)
Hours: 3.9 | Posted in Wing & Tail Joins |
10th
November
2010
Lots of work at work, and more work when I come home at night…the only plane progress has been unpacking the replacement angle stock for the tank bracket (along with the 4-channel dimmer I ordered as long as I was paying for shipping). However, I did find a picture of my seat on Classic Aero’s website today…they’ve been posting many recent customer shipments in a gallery to show a broader range of designs, and they took a far better photo than I did. Haven’t sat in them yet, but they sure do look nice:
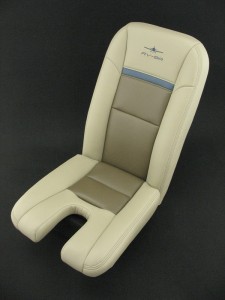
Seat details for future reference:
- Classic Aero Aviator style, “horizontal stripe” design
- Ultraleather fabric
- Papyrus edge color
- Walnut center color
- Diplomat Blue stripe color
- Embroidery matches blue stripe color
- Built-in seat heaters
- Papyrus color stick boots (not shown)
- Front carpet in Latte color (not shown)
- Aileron pushrod boots and glareshield pinch welt (not shown)
Posted in Cabin & Interior |
1st
November
2010
Another attempt to bend the fuel tank attach brackets; clamped the first one tight in the vise using a radiused hardwood block as a sort of mandrel, following the lead of a few who have gone before. Wailed on that sucker with a big hammer and got about half the required bend; further whacking only served to flex it down into the top of the vise and gouge it up. Bugger. Tried soemething different on the second one: used some bits of aluminum angle to fix it in between the vise jaws, with one leg on each jaw, and slowly cranked down. A couple tries had the bend spot on. No more material left that’s big enough to make another bracket to replace the gouged up one, so that’ll have to be ordered from Van’s (this being part of the stuff that holds the wing on…). What’s one more shipping delay, right?
In happier news…the seats arrived this morning! I was almost out the door for work when the UPS truck pulled up, and offloaded a couple big boxes. There they sat while I put in a day’s work, and tonight we popped them out to admire. They turned out nicely, I think. Back in the box for now for safekeeping.
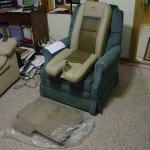
Hours: 1.2 | Posted in Wing & Tail Joins |
30th
October
2010
Attempted to finish up the final tasks around mounting the wings tonight, in an effort to get at least one garage bay open for parking again. First up was drilling the wing root fairings, which turned out to be relatively easy. The fairing is pre-drilled all along it’s length, and the holes match up with open holes in the wing top skin. Once in place, the holes are match-drilled into the edge of the fuel tank skin. Then the bottom fuselage skin is drilled to the wing skin, with the aid of guide lines drawn on the wing skin before mating the wings. I first drilled all the holes to #40, then enlarged to #19 for the #8 screws. Once the wings are removed, these holes will be prepped and nutplates attached.
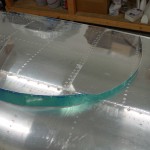
The other remaining task was to fabricate and install the F-996A fuel tank attach brackets, which mate with the beefy angle piece built into the inboard nose of each fuel tank. Cutting and shaping these was straightforward if tedious (due to the 3/16 thickness of the angle), but the bending appears to be the tough part…clamping them in the vise and using a crescent wrench (a la longeron bending) did nothing, nor did whacking them with a hammer and wood block, or attempting to compress them in the vise (as we do in other places when narrowing the spread of a piece of angle). Reading the typical online sources, it appears I just need to hit them harder, so that’ll be tomorrow’s task. Tonight, I’ll double-check that everything is done that needs doing before pulling the wings.
Hours: 3.8 | Posted in Wing & Tail Joins |
24th
October
2010
No work on the project for nearly a month, though it’s been near in thought. Times have been busy at work pushing toward completion of a complete remodel of our audio production studios, and life has happened in other areas, as well. In the meantime, Vertical Power shipped me the new blank box for the VP-X Pro (the other one is on the way back), and I bought some vise-grip clamps for drilling the rear spars. That’s about the entire progress that was made on the project; the upside is that the credit card bill this month will be gloriously small.
Tonight I pushed over the next hurdle, hoping that things will mellow a bit for at least a few weeks and allow some work time…the engine and interior should be coming early next month, and the icy season is dead ahead, so I need to get the wings off and restore some garage parking.
After checking the fuselage for level fore-aft and laterally, I trimmed a block of hardwood to a bit larger than the spacer required for finding the wing incidence, and fine-tuned it’s length with the disc sander. With the block of wood securely taped to a 4′ level at the correct distance from the end, and a bucking bar taped at the far end to hold it on the wing, I was ready. Setting the wing incidence was easy; both were very close to start with, requiring only a small adjustment upward, and a push to be sure the rear spar was fully seated in the “hand” of the fuselage. Clamped down and measured in several locations along the wing, then marked the infamous 5/8″ edge distance on the spar stubs (a piece of scrap filed to 5/8″ made marking easy…I actually cheated for extra safety margin and used a 21/32″ strip, and the width of the marker line made it more like 11/16″…).
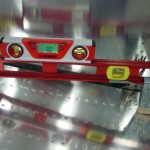
Satisfied with the rigging, I test-fit the flaps as suggested by Van’s in their incidence drilling guide. Both flaps required filing off a small portion of the inboard nose skin to clear the spar stub for full retraction, but the bottom skin tucked nicely against the fuselage bottom. Flaps off, I went in and re-read the drilling guide from Van’s. A couple more measurements, and it’s time to get on with the drilling. “Nothin’ to it but to do it,” as they say.
The actual deed was done easily. A long #30 bit and a drill guide made from a block of oak set the pilot holes in the center of the edge-distance box. Stepped up the holes with a series of drills to final size: #30, #20, #10, .250, .295, then the .3115 reamer for final fit on the AN5 bolt. A touch of deburring and in went the bolts. Done.
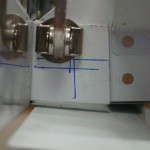
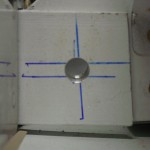
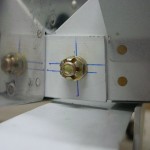
Hours: 2.8 | Posted in Wing & Tail Joins |
26th
September
2010
Hit the major goal for this weekend with a short work session: the wings are attached for the first time. I was able to use a rolling chair with the back removed as a fixture to handle the wings for joining them to the fuselage; along with a sawhorse and a 2×4, it went pretty easily. I ground the threads down on my four hardware-store bolts to use as drift pins, tapping them in with a rubber mallet when the holes were closely aligned. After the first fitting, I had to remove the wings to file a bit off the rear spar stubs to remove a touch of forward sweep. On the second fitting, the forward sweep has been reduced to less than 1/16″ per side…I could call that good, or choose to pull them again and file the stubs some more. I’ll also read through Van’s wing attach guide document once more to be sure of what happens next.
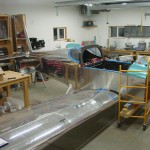
Hours: 2.1 | Posted in Wing & Tail Joins |
23rd
September
2010
Finished up the wing skin riveting tonight (excepting the nutplates for the inspection covers). I’m clearly not as good of a left-handed riveter, as I managed to put an ugly ding in the right wing bottom skin by slipping off the bar. Sigh. Smoothed it out a bit and will either leave it alone or use some filler before paint to level it.
Cleaned the shop up and made room for the wing attach, hopefully coming up this weekend. The rudder & elevators were removed and stored, then the fuselage was turned into the center of the shop and leveled in both axes. Measurements were taken, and it appears that there is enough room to fit the wings without having to clear the piles of stuff from the side walls. The canopy was also removed, as it would hit the garage door opener if opened fully, and having it off will give better access for leaning over to reach the spar bolts.
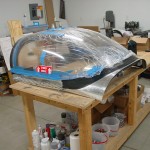
Next step: read up on what needs to be done prior to the wing attach (so far: trim rear spar stub, trim fuel/vent lines, and some sort of marking for the root fairing holes…what else?)
Hours: 2.4 | Posted in Skin Panels, Wing & Tail Joins |
14th
August
2010
Allison helped rivet the aft skins to the fuselage in an evening session today, while I laid inside the tailcone to buck. A couple pieces of egg-carton foam made it bearable, almost comfortable. After riveting the skins, I bolted the shoulder harness anchors to the longerons, as long as I was back there. Also riveted the canopy stop brackets to the longerons.
I did end up–as I have read others do–using three blind rivets on each side of the aft skins, at the forward end where the heavy angle piece under the roll bar blocks access to the rivet tails. The pride of solid rivets there wasn’t worth the frustration of the impossible bucking access. They can always be filled with a dab of epoxy before paint and no one will ever know.
(edit: I see now that those blind rivets, CCR264SS-3-4, which I pulled from a “Cherry rivets” bin at Oshkosh, are actually soft rivets intended for installing nutplates. I hadn’t realized the depth of the Cherry rivet catalog, and bought those on impulse, thinking of this spot. I’ll research and order some correct rivets that would be appropriate here, perhaps a CR3214-4-x, and remove/replace these when they arrive…)
(edit 2: The CR3214-4-x rivets have been successfully used by others, according to the wisdom of the internet, but they are reportedly expensive, and the common suppliers only stock them in 100-pack minimums. I did find where someone else had this same dilemma and ended up using the “nutplates” rivets that I just installed. I flirted with the idea of leaving them in place, since they would be easy to replace later if/when needed. But, I did bite the bullet and order some of the spendy rivets, since VAF threads indicate they may come in handy when closing up the forward top skin as well. Genuine Aircraft Hardware is stocking them in 10-packs, though they are definitely made of precious metal, looking at the price…)
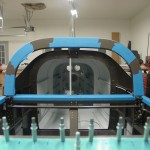
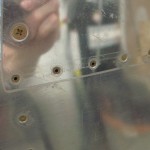
Hours: 4.2 | Posted in Upper Fuse & Skins |
1st
August
2010
Nothing much accomplished today…cut a piece of hinge and messed around with ways to mount the flap position sensor I picked up at OSH. I will need some adel clamps to fashion a pivot point on the flap actuator to attach the sensor arm. Thought about the canopy, and electrical systems…
Hours: 1.0 | Posted in Cabin & Interior |
16th
July
2010
Another session of disparate small tasks. Perhaps the less focused building sessions are what causes the feeling of being overwhelmed that builders seem to get in the end stages; there’s a hint of that here. I’m trying to wrap up some odds and ends around the fuselage before diving into the canopy work.
- Finished drilling the roll bar brace for the cover plate, and drilled it for nutplates. I didn’t have enough #6 nutplates to do all the holes, so I left a few easily accessible ones without; they’ll be easy to stick in later, when my shipment from Van’s arrives next week.
- Primed and painted the cover plate…wow, is the spray-can primer I picked up easy to use, it will come in handy for one-off bits from here to the end.
- Riveted and bolted the roll bar to the fuselage. Clecoed the structure aft of the baggage bulkhead solidly together before bolting this on, to set the correct location fore/aft. It’s difficult to get any large tools in there, and fitting the washers and nuts is a trick, too–the tool that I called the “grabber” growing up (I’m sure it has a real name…) came in very handy here, to hold the washers and nuts in the right place.
- Applied UHMW tape to the inside of the canopy latch angles, riveted them to the side skin, and assembled the rest of the latch mechanism.
- Put a strip of UHMW tape across the top of the flap motor housing, where the canopy latch tube rubs slightly.
- Mixed up a small batch of proseal and stuck the NACA vents to the side skins. (Forgot to put the screens on the fuel vents while I had it mixed up…darn!)
- Made an antenna drill template, and drilled for the Com1, Com2, and Transponder antennas. Very handy that they all use the same mount spacing (though beware, the Com antennas are longer fore/aft than the transponder). These are from DeltaPop, and though I can’t yet comment on their performance, they’re reasonably priced and quite attractive. Other users report good things, including the folks at NavWorx, who recommended the ADS-B antenna for use with their boxes (I have that antenna too, and will be prewiring for the NavWorx transceiver…). There is also an APRS antenna in the works, I believe.
- Drilled a hole for a wee rubber grommet in the aft bulkhead, to feed wiring to the rudder for nav/strobe lights. I ordered a 100-pack of 1/8″ ID grommets from McMaster Carr, because that’s the smallest pack they sell; I’m set for life now. I discovered later that SteinAir sells a kit with an assortment of different sizes… I also ordered a bunch of different tie-wrap bases including the regular square-base type and some other useful-looking ones like thru-hole mounts; having the different kinds on hand will come in handy for the electrical installation.
- Spread out a big piece of paper and drew a crude representation of an airplane on it, and looked at laying out the various wire runs through the fuselage. I want to get the pieces aft of the baggage bulkhead in place, so I can close up the aft fuselage.
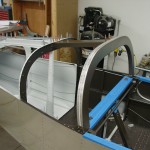
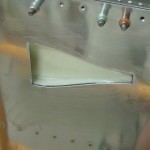
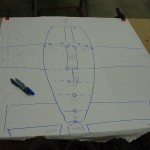
Hours: 4.3 | Posted in Cabin & Interior |