Spent the morning at the Minnesota Wing meeting, talking and looking at a local RV-7 that was recently finished, which provided some good inspiration to move ahead on the FWF stuff; also had the change to talk to folks about some open questions: mufflers and heater boxes, seat heat switch location and wire routing, transition training, and so on. Notes to self: the Torx screws on tips and hex-heads for interior panels look nice; heated seat wiring can be run out underneath the flap motor housing, and the cushion cables are long enough to reach; relays can go in the flap housing with switches on the crossbar (though they are hard to reach in flight, it cuts down on wiring run through the center section).
Back in the shop this afternoon, my goal was to get most of the firewall components installed and ready to hang the engine tomorrow. Number one on the list was the heater boxes. I chose to mount one in the center, feeding into the stock diffuser box; the second one is placed on the passenger side, far outboard. I oriented that one with the outlet (which dumps the heated air when the valve is closed) pointing down, thinking that it would provide better airflow to the lower cowl exit. This meant that the box had to be up the firewall some amount to allow room for the control cable to exit below it, so it ended up next to the battery. Hopefully I don’t regret this, but I’ve been pondering it for several weeks and it was time to make a decision and get on with it. I think in this location, it would be easy to add a flange on the cabin side if desired later, to direct the air from that vent to an eyeball or glareshield vent. Everyone I talked to who has the muffler exhaust, or has flown a plane with it, is pleased with it and says that there is more than enough heat output, which will be a good thing.
I used a 2″ hole saw (buying the kit of quality hole saws was a good move, as I’ve had zero difficulty cutting the stainless) with the drill motor slowed down (regulator set ~35psi) to make the holes, and used the doubler for a template to drill the mounting holes. I decided to use #8 screws rather than the #6 called for in the plans, mostly because I had truss-head #8 screws, and only countersunk #6 screws. And, rather than using nuts on the backside, I put nutplates on the doubler to allow for easier one-man installation and future service. These are the triangular heat boxes from Robbins Wings, which have a stainless steel hinge and flapper, with an aluminum box. The theory being that if there was a fire, the box might melt away, but the flapper, being stainless, would remain to cover the 2″ hole in the firewall. This is a variation on the all-stainless box, and seems good to me. They include the doublers, and are set up for control cables on the engine side.
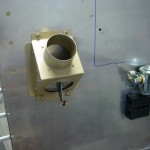
With the heat boxes in place, the next order of business was to install the firewall recess. Besides removing the top skin, this meant mixing up the firewall sealant, Flamemaster CS 1900. It is a two-part concoction, similar to Proseal, but part A is a very stiff paste and part B a thin liquid; it is difficult to mix, and remains very thick after mixing. The data sheet indicated that it could be thinned for application, including brushing, by use of ketone solvents. A little research told me that acetone is a basic ketone solvent (which saved me a trip to the store for MEK), and it took a lot of acetone to get it to a workable consistency. Put it in a freezer bag for application, same as I did with the Proseal on the fuel tanks. After wiping all the parts down with solvent as instructed, I ran a bead between the recess and the firewall and clecoed it in place. I let that begin to set up while I sealed and installed both wiring pass-thrus, and sealed around the brake reservoir penetration. Then I went back and riveted the recess in place, and sealed around the edges and in the seams and corners, filling the holes at the corners with a blob of sealant. Cleaned up the mess and called it good. Once the recess was in and the sealant had tacked, I bolted and torqued the battery box and heater boxes. No pictures of the sealing process, because it’s hard to use the camera when your hands are covered in black goop. The copius acetone thinning didn’t seem to affect it’s ability to cure, and it skins over fairly rapidly after dispensing.
Once the sealing was complete and cleaned up, I installed and clamped the outer firesleeve on the wiring passthrus, as it needs to be in place before the wires are run, and I didn’t want to forget it later and have to take all the wires out to install it. (Like flaring tube without a B-nut, or soldering a connector without the backshell — not that I’ve ever done either of those…)
Engine mount is next…had to fit and remove a couple times to work on the nose gear bolt clearance, and I ended up putting a little “dent” in the firewall behind the gear leg to shift it aft and provide clearance for the bolt & nut. I’ve read that this is not uncommon. I also had to file a bit more off of the lower fuel pump nutplate to clear the lower mount tube, and I filled both nutplates with firewall sealant, since I’m not using them (this pump location is used only for carbureted engines; I wasn’t sure whether I would have carb or FI when I built the firewall, so I put the doubler & nutplates in). As of now, the engine mount is bolted up, but not yet torqued, as I expect to need to remove it (along with the engine) one more time to drill and install all the cable and plumbing penetrations, once I figure out where they need to go.
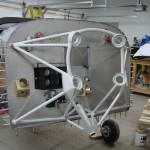