17th
May
2009
With the leftover Proseal from the left tank, I decided to install the AOA wing components, since they need sealant between the fittings inside the wing and the skin of the leading edge, in which a #60 hole is drilled for the actual port. The install is fairly straightforward, as AFS provides measurements for properly locating the upper & lower ports. They are installed at the same chord location, but offset a few inches from each other spanwise. On the 9 wing, they end up behind the cutout for the leading edge lights, but the AFS guys indicate that’s no problem. In addition to the two ports, a small hole is drilled in the bottom skin so that a plunger can be inserted to actuate the quick-drain at the bottom of the upper port (allowing any water which may have entered via the upper port to be drained from the system).
Of course, nothing is ever as easy as it seems; the port fittings install with two countersunk screws, which can fit into a #30 dimple (though they’re not actually #30 screws, it seems). Drilling them was easy (remove the brass barb from the lower port fitting, and use it as a guide to mark the hole locations). However, having already installed the leading edge to the wing, dimpling those holes was proved interesting. There is no way to get a squeezer in there, as the end rib is in the way, plus the ports are 4.75 and 7.5 inches inboard from the skin edge. I experimented with various tools, assemblies of tools, and different ideas without success. I finally decided to do what is done on the rear spar: dimple, then “ream out” the dimple. I dimpled to #40 with the pop-rivet dimplers, then used a #30 countersink in a microstop cage, going one step at a time deeper until the screws sat just flush with the skin. Having already dimpled the skin prevented the countersink from having to remove too much material.
It may not be the perfect way to install these, but they’re in, and it’s what I had available. Word to the wise: figure out these locations when you have the assembly clecoed together for the first time, and dimple them with a C-frame type tool! Either that, or buy the #30 pop-rivet dimplers that I now see are available. I don’t know if these will be needed elsewhere on the plane, but I may toss in a set with my next order of something, just to have around in case. It’s a solution in need of a problem just like the one I had tonight.
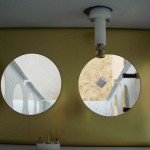
After all that, I even found time to tidy up the shop and put away the various tools that have been laying around.
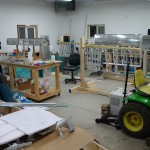
Hours: 2.1 | Posted in Accessories & Mods |
17th
May
2009
Concert season is winding its way to a close, lawn is mowed and the garden is ready for planting; finally a chance to get back into the shop for some quality Proseal time. Finished up the left tank today, with only one major moment of frustration…
Before sealing things up for good, I gave as much of the tank as I could see an look-over with light & inspection mirror, with a special eye toward the skin-baffle joint and the four outside corners that received the “blobs” of sealant. Everything looks good, but that can mean nothing–the proof is in the leak test. Ran two beads of sealant from a syringe around the access plate opening, and clecoed it in place without trouble, then replaces clecoes with screws one-by-one in a star pattern, like lug nuts or head bolts, also twirling each screw in Proseal, and dabbing a bit in the hole, so that I ended up with a bed of sealant squeezed out around each screw head.
When the access plate was sealed on, all the screws in place, I began to go back with the torque wrench to check their tightness…that’s when it happened. The second screw I torqued snapped off. My smallest extractor was too big, so out came the other 11 screws, and a vise-grip was the tool of choice to run the broken screw fragment out the back of the nutplate (plan B would have been to drill off and replace the nutplate, but that has a greater risk of contaminating the inside of the tank with aluminum shavings). Cleaned up the sealant with acetone, and did it all over again. I used the screws that had been set aside for the second tank, as I didn’t know which of the 11 screws was the first one I torqued–I didn’t want to have another screw snap off, if I’d streched the first one. I’ll pick up some replacement screws for the second tank; maybe even the hex-head cap screws some folks like to use.
I’ve heard of people over-torquing these AN fasteners many times, which is why I bought an in-lb wrench to use…I guess 20-25 in-lb is still too close to the bottom of it’s adjustment range to be accurate. On the second try, I didn’t use the wrench, electing to use instead the ancient “gudentite” torque system. (I did use the wrench on a bolt clamped in the vise, to get a feel for the required amount of torque…I’m confident I’m acceptably tight. If these were structural fasteners, I’d try to find a decent torque screwdriver, but they didn’t have any at the stores I visited when looking for the in-lb wrench.)
With the access plate fun out of the way, I encapsulated the heads of all the rib-baffle and skin-baffle rivets. After a few days to cure, this tank will be ready for pressure test.
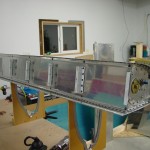
Hours: 2.6 | Posted in Fuel Tanks, Wings |