Didn’t get part of Friday off from work as I’d hoped, but today I proceeded with the weekend plan of highlighting a bunch of items on the punch list, and knocking them off…
Mixed up a batch of firewall sealant (don’t smell that stuff…wow) and sealed the perimeter of the firewall sides and bottom, and a fillet in the lower corners. The top curve will get done later when the top skin is put on. Let that tack up, then clecoed & riveted the sides and bottom, along with the shims, hinges, and camloc strips. By moving the exhaust stacks and using a variety of yokes, I was able to easily squeeze every rivet but the centerline bottom rivet, which was unsqueezable with any yoke from any angle. That hole now sports a pulled rivet. Once the camloc strips were on, the camloc receptacles were added. Done.
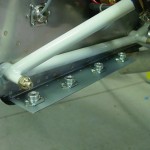
With the lower edge of the firewall complete, I added the metal portion of the fuel pump vent line. Done.
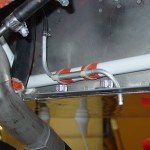
The metal fairing strips that run underneath the HS were next; drilled and tapped the appropriate holes in the aft longerons, drilled the strips, and test fit. To see how the fit was, I added the HS back on for a moment, and marked the trims that needed to be made. After several iterations, I had the 1/32 to 1/16″ gap called for in the plans, so the strips were primed. Still need to countersink the strips, but Almost Done.
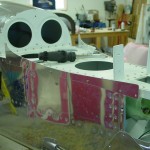
Removed the canopy strut attach blocks and primed/painted them. While they were drying, I removed the blue tape that has been covering the canopy decks; underneath, I found (as I suspected) that some of the adhesive had become gummy, so that’ll have to be washed up. Later, reinstalled the strut pivots, and reinstalled the assembly to the canopy decks. Done.
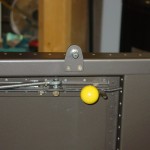
Big job of the night: redo the intake studs in the engine sump so the nuts have enough threads protruding. This required moving the exhaust stacks (again) and partial disassembly of the entire fuel servo/control cable works — not an easy task due to the limited room to swing a wrench; several of the bolts can only be turned one flat (1/6 turn) at a time. Eventually, though, it was off, the studs removed, holes cleaned, and reinstalled studs to the correct depth. Not much was really needed, only 1/8″ or so on each one. Some of them ended up being a little longer than necessary, but there’s plenty of thread and the nuts are not bottomed, so all is well. You don’t want to bottom the stud out in the blind hole, as it will stress the threads and can cause them to fracture. I used a torque wrench to verify that the driving torque requirement was met, and installed with red loctite per the AFP manual. Much reassembly later, we’re back in business, and the nagging “that’s not right yet” of those studs is gone. Verified stop-to-stop movement of throttle and mixture. Done.
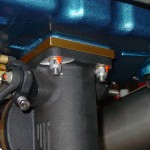
Enlarged the drain holes on the fuselage to #19 based on talk that the #30 hole isn’t big enough, and (especially if any gunk is present) the surface tension of water will prevent it from draining. Also added a drain hole at the lowest point of the fuselage (which is under the seats, and not at a bulkhead), and one under the fuel pump area.
Placarded the alternate static valve installed the other day, and remade the fuel purge and center cabin heat placards with white on black, which looks nicer on the black panel. Also made black on clear labels for the extra PTT buttons on the fwd canopy decks, and for the pilot’s stick functions (PTT, Trim Up/Dn, and AP CWS)…I expect those will fall off over time and use, but my understanding is that it’s better to have everything labelled to the point of excess at inspection time.
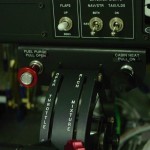